Plastic Injection Mold Design Florida is a complex process that involves numerous variables that can affect the final product. Understanding these critical factors can help you avoid costly injection molding defects like sink marks, flow lines, and warping.
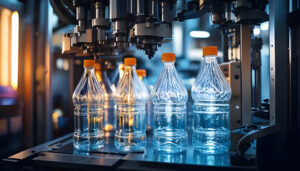
Wall thickness is an important injection molding design consideration. Uniform walls promote better material flow and reduce the risk of sink, molded in stress, and differential shrinkage.
Injection molding is a highly precise manufacturing process that demands considerable skill and attention to detail. For example, the gate—the doorway through which molten plastic enters the mold cavity to form your final product—plays an essential role in controlling the flow of the polymer, ensuring that the part comes out strong and accurate. But a poor gate design can easily lead to production defects, such as uneven filling and warpage. This article explores the different types of gates used in injection molding, how they work, and some practical tips on improving gate design for more successful results.
During the design phase, plastic injection manufacturers should carefully consider where and how to place the gates. The type of gate and its location influences the flow of molten plastic into the mold cavity, as well as the appearance of the molded part. For instance, a poorly placed gate can cause flow marks or burn marks, which are visible in the surface of the molded plastic and affect surface finish and strength. Injection molding companies can minimize these defects by avoiding cosmetically undesirable locations for the gates.
The choice of the type of gate is also influenced by its effect on manufacturing costs. Certain gate types require more complex tooling, which can increase upfront costs. However, choosing a gate type that reduces post-processing operations can save money in the long run. In particular, a hot-runner system can significantly reduce scrap by eliminating the need to trim the gates manually.
There are four common gate types for injection molds: edge, sub, hot-tip, and pin. Edge gates, which are positioned near the part’s parting line, leave a scar on the surface of the finished product. Sub gates, such as banana, smiley and tunnel gates, can be positioned away from the parting lines, offering greater flexibility in the design of the injection mold. Finally, pin gates are positioned on the mold’s B-side and near the ejector pins. These gates are also able to be trimmed automatically.
Draft Angles
The draft angle is the angle or taper on the wall of a plastic part feature. It is one of the most important design guides in plastic injection molding. If a plastic part is not properly designed with draft angles it will have issues during ejection from the mold. When a product is molded without draft angles, the cooled plastic shrinks around the core and causes friction that makes it difficult to be ejected from the mold. This friction also causes damage to the ejector pins that push into the product during the ejection process. Draft angles help reduce this friction by allowing the ejector pins to move into the plastic more easily, which also saves time and money during production.
The size of the draft angle is based on several factors, including wall thickness, material shrinkage, post-production finishing requirements, and more. For example, hard plastics typically require larger draft angles than soft plastics because of their stiffness. The slope of the draft angle is also important, as a steeper angle can make it easier for the ejector pins to move through the wall and into the cavity of the product.
Another factor in determining the draft angle is the product’s overall dimensions. Larger products will need a bigger draft angle to facilitate ejection because of their weight. In addition, if the product has any sharp edges or corners, it should be rounded to avoid the need for tight tolerances in the mold. Rounded corners are also more forgiving during ejection and can reduce the chance of breaking the product during extraction.
If a plastic part’s functionality requires that it have a vertical surface that cannot be accommodated with a draft angle, other solutions like side-action cores can be used to overcome this challenge. However, these structures can be expensive to build and add to the overall cost of the product.
Draft angles are often calculated with the help of simulation software, but they can sometimes be influenced by other factors, such as the surface finish of the product and its overall shape. For this reason, it is important to include draft angles in the initial product design phase to minimize the need for redesigns later in the project and reduce cycle times.
Cooling System
Cooling is a critical part of the injection molding process, making up 60%-70% of the total cycle time. The right cooling system will help reduce this percentage, allowing for faster production and increased quality.
The cooling system is comprised of a series of channels, or veins, that guide the cooling medium throughout the mold. Strategically placed and designed, these cooling channels ensure uniform cooling, preventing product defects, as well as shortening the cycle time.
A cooling channel’s diameter should be consistent throughout the mold, as variations can lead to uneven coolant distribution. This can cause some areas of the mold to be cooled more quickly than others, which can result in warping or breaking. To counter this problem, it’s important to locate cooling channels close to the thickest parts of the mold.
To maximize the cooling effect, it is also a good idea to place a cooling channel next to each gating hole. This allows for better cooling of the molten plastic around the gate, resulting in less warping and breaking during ejection.
During the cooling process, the heat from the molten plastic that entered the mold through the gate is transferred to the cooling water pipes through heat conduction, and then carried away with the liquid by thermal convection. A small amount of the heat that was not transferred to the cooling water pipe continues to conduct in the mold until it reaches the surface of the mold and is drawn away by air.
To avoid contamination, a good cooling system will incorporate a heat exchanger and chiller that manages the temperature of the cooling water and keeps it at a constant rate. This will help to prevent oxidation and mineral deposits in the cooling lines, which can significantly decrease efficiency. The cooling system is also equipped with pumps and flow regulators that help to maintain proper pressure and flow, ensuring the coolant reaches all areas of the mold. In addition to this, baffles and bubblers can be used to enhance cooling in hard-to-reach areas of the mold. These devices are inserted into the mold and draw heat from specific areas, vaporizing and condensing as they reach the cooling channel, thus increasing the cooling capacity of that area.
Parting Line
The parting line is one of the most significant components in a quality injection molded plastic product. The location of this line affects a part’s overall appearance and structural integrity. It is also important to consider when determining how a part will be ejected from the mold.
A quality parting line must be positioned so that it is hidden from the product’s visual perspective, while remaining strong enough to prevent a split during the injection molding process. This requires a careful balance of aesthetics, strength and cost. Ideally, the parting line would exist on a flat plane and be easily hidden, but that is often not possible due to the complexity of many products’ geometry. The location of the parting line must also allow for a proper fit with other parts within the tooling, as well as clear features on the outside surface of the product, when it is injected and cooled. This is especially crucial for injection molded parts with threads, fasteners or other components that may require an additional step to remove them from the part.
This complex process is made even more difficult by the need to account for shrinkage of the injected polymer. This characteristic is dependent on the type of plastic used and cannot be predicted with accuracy until the actual mold is constructed. This makes it imperative to plan the design and layout of the parting lines before the initial build begins, as it is difficult to make changes once production has begun.
Injection molding is an inherently challenging process for manufacturers, as it is not uncommon to see mistakes at every stage of the manufacturing cycle. Despite these difficulties, the skilled designers are able to provide high-quality, accurate injection molded products for our customers. To do this, we take the time to fully understand our customers’ needs and the product they are requesting before beginning the design and manufacturing process. We also work with our customers to keep them up-to-date on the latest advancements in injection molding technology and processes, ensuring that we remain a leader in our industry.